铝合金氟碳漆施工工艺可保护铝合金材料,提升其装饰性与耐久性。以下是详细的工艺流程:
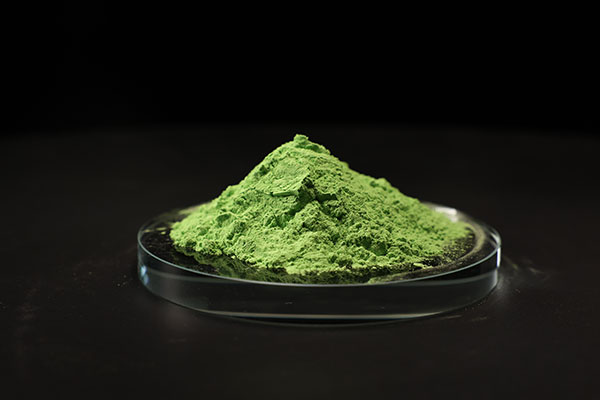
施工前准备
材料准备:
铝合金基材:确保其质量符合相关标准,表面应平整、无裂缝、无砂眼等缺陷。
氟碳漆:根据工程需求和设计要求,选择质量可靠、性能稳定的氟碳漆产品。同时,配套准备相应的稀释剂、固化剂等辅助材料,且这些材料应与所选氟碳漆具有良好的兼容性。
工具设备准备:
表面处理工具:包括电动角磨机、砂纸、钢丝刷等,用于对铝合金基材表面进行打磨、除锈等处理。
喷涂设备:常用的有空气喷涂枪、高压无气喷涂机等。空气喷涂枪适用于对装饰性要求较高的场合,能够获得均匀、细腻的漆膜;高压无气喷涂机则适用于大面积施工,具有较高的喷涂效率和较好的漆膜质量。同时,还需准备相应的空压机、气管、喷枪清洗设备等辅助工具。
测量工具:如膜厚仪、粗糙度仪等,用于在施工过程中对漆膜厚度、基材表面粗糙度等进行测量和监控,确保施工质量符合要求。
施工环境准备:
温度:施工环境温度应保持在5℃-35℃之间。当温度过低时,氟碳漆的干燥速度会明显减慢,甚至可能出现无法干燥的情况,影响漆膜的性能和质量;当温度过高时,漆液的溶剂挥发速度过快,容易导致漆膜表面出现橘皮、针孔等缺陷。
湿度:空气相对湿度应控制在85%以下。湿度过高时,空气中的水分容易在铝合金基材表面凝结,影响氟碳漆与基材的附着力,同时也可能导致漆膜在干燥过程中出现发白、起泡等现象。
通风:施工场所应保持良好的通风条件,以确保空气中的漆雾和溶剂蒸汽能够及时排出,降低施工环境中的有害物质浓度,保障施工人员的身体健康,同时也有利于漆液的干燥和固化,提高漆膜的质量。
铝合金表面处理
脱脂处理:铝合金表面通常会有油污、油脂等污染物,这些污染物会影响氟碳漆与基材的附着力,因此需要进行脱脂处理。常用的脱脂方法有有机溶剂脱脂、碱性溶液脱脂和乳化液脱脂等。
有机溶剂脱脂:利用有机溶剂对油脂的溶解作用来铝合金表面的油污。常用的有机溶剂有丙酮、丁酮、甲苯、二甲苯等。有机溶剂脱脂的优点是脱脂速度快、效果好,对各种油脂都有较好的溶解能力;缺点是有机溶剂易燃易爆,具有的毒性,对环境有污染,且成本较高。在使用有机溶剂脱脂时,应注意通风良好,避免明火和静电,操作人员应佩戴防护手套、口罩和护目镜等防护用品。
碱性溶液脱脂:通过碱性溶液与铝合金表面的油污发生皂化反应和乳化反应,将油污。常用的碱性溶液脱脂剂主要由氢氧化钠、碳酸钠、磷酸三钠、硅酸钠等碱性物质和表面活性剂组成。碱性溶液脱脂的优点是脱脂效果好,成本较低,对环境的污染相对较小;缺点是碱性溶液对铝合金有的腐蚀性,尤其是在高温、高浓度和长时间浸泡的情况下,容易导致铝合金表面出现腐蚀坑、变色等缺陷。因此,在使用碱性溶液脱脂时,应严格控制脱脂液的浓度、温度和浸泡时间,一般脱脂液的浓度为3%-10%,温度为50℃-80℃,浸泡时间为5-20分钟。脱脂后,应立即用大量清水冲洗铝合金表面,将残留的脱脂液冲洗干净,然后进行中和处理,以防止铝合金表面生锈。
乳化液脱脂:乳化液脱脂是利用乳化剂的乳化作用,将铝合金表面的油污分散在水中形成乳浊液,从而达到油污的目的。乳化液脱脂剂主要由乳化剂、有机溶剂、缓蚀剂、助溶剂等组成。乳化液脱脂的优点是脱脂速度快、效果好,对各种油脂都有较好的乳化能力,且对铝合金的腐蚀性较小;缺点是乳化液脱脂剂的成本相对较高,且乳化液中的有机溶剂易燃易爆,对环境有的污染。在使用乳化液脱脂时,应注意控制乳化液的浓度、温度和浸泡时间,一般乳化液的浓度为2%-5%,温度为40℃-60℃,浸泡时间为10-30分钟。脱脂后,应立即用大量清水冲洗铝合金表面,将残留的乳化液冲洗干净。
酸洗处理:经过脱脂处理后的铝合金表面,可能还会残留一些氧化皮、锈迹等杂质,这些杂质会影响氟碳漆与基材的附着力,因此需要进行酸洗处理。酸洗处理是利用酸溶液与铝合金表面的氧化皮、锈迹等杂质发生化学反应,将其溶解,从而使铝合金表面露出新鲜的金属表面,提高氟碳漆与基材的附着力。常用的酸溶液有硫酸、盐酸、硝酸、磷酸等。在选择酸溶液时,应根据铝合金的材质、表面状态和杂质种类等因素进行综合考虑,选择合适的酸溶液和酸洗工艺参数。
硫酸酸洗:硫酸是一种常用的酸洗溶液,其优点是价格便宜,货源广泛,对铝合金表面的氧化皮、锈迹等杂质有较好的溶解能力,且酸洗后铝合金表面的光泽度较好。缺点是硫酸的腐蚀性较强,尤其是在高温、高浓度的情况下,容易对铝合金表面造成过度腐蚀,导致铝合金表面出现腐蚀坑、变色等缺陷。因此,在使用硫酸酸洗时,应严格控制硫酸溶液的浓度、温度和酸洗时间,一般硫酸溶液的浓度为10%-20%,温度为40℃-60℃,酸洗时间为5-20分钟。酸洗后,应立即用大量清水冲洗铝合金表面,将残留的硫酸溶液冲洗干净,然后进行中和处理,以防止铝合金表面生锈。
盐酸酸洗:盐酸也是一种常用的酸洗溶液,其优点是对铝合金表面的氧化皮、锈迹等杂质有较强的溶解能力,尤其是对铁锈的溶解速度较快,且盐酸的挥发性较强,酸洗后铝合金表面的残留酸液容易挥发,对后续的处理工艺影响较小。缺点是盐酸的腐蚀性较强,对铝合金表面有的腐蚀作用,尤其是在高温、高浓度的情况下,容易导致铝合金表面出现腐蚀坑、变色等缺陷。同时,盐酸的挥发性较强,在酸洗过程中会产生大量的酸雾,对环境有污染,且对操作人员的身体健康有的危害。因此,在使用盐酸酸洗时,应严格控制盐酸溶液的浓度、温度和酸洗时间,一般盐酸溶液的浓度为5%-15%,温度为30℃-50℃,酸洗时间为3-15分钟。酸洗后,应立即用大量清水冲洗铝合金表面,将残留的盐酸溶液冲洗干净,然后进行中和处理,以防止铝合金表面生锈。同时,应加强通风措施,减少酸雾对环境的污染和对操作人员身体健康的危害。
硝酸酸洗:硝酸是一种强氧化性酸,在铝合金酸洗中,硝酸不仅可以溶解铝合金表面的氧化皮、锈迹等杂质,还可以在铝合金表面形成一层致密的氧化膜,提高铝合金表面的耐腐蚀性和与氟碳漆的附着力。硝酸酸洗的优点是酸洗速度快、效果好,对铝合金表面的各种杂质都有较好的溶解能力,且酸洗后铝合金表面的氧化膜质量较好,能够提高铝合金表面的耐腐蚀性和与氟碳漆的附着力。缺点是硝酸的腐蚀性较强,尤其是在高温、高浓度的情况下,容易对铝合金表面造成过度腐蚀,导致铝合金表面出现腐蚀坑、变色等缺陷。同时,硝酸是一种强氧化性酸,在酸洗过程中会产生大量的氮氧化物气体,对环境有严重的污染,且对操作人员的身体健康有的危害。因此,在使用硝酸酸洗时,应严格控制硝酸溶液的浓度、温度和酸洗时间,一般硝酸溶液的浓度为5%-15%,温度为30℃-50℃,酸洗时间为3-15分钟。酸洗后,应立即用大量清水冲洗铝合金表面,将残留的硝酸溶液冲洗干净,然后进行中和处理,以防止铝合金表面生锈。同时,应加强通风措施,安装废气处理设备,对酸洗过程中产生的氮氧化物气体进行处理,达标后排放,减少对环境的污染和对操作人员身体健康的危害。
磷酸酸洗:磷酸是一种中强酸,在铝合金酸洗中,磷酸对铝合金表面的氧化皮、锈迹等杂质有较好的溶解能力,且磷酸在铝合金表面形成的磷酸盐膜具有较好的耐腐蚀性和与氟碳漆的附着力。磷酸酸洗的优点是酸洗速度相对较慢,对铝合金表面的腐蚀作用较小,能够避免铝合金表面出现过度腐蚀的现象,且酸洗后铝合金表面形成的磷酸盐膜质量较好,能够提高铝合金表面的耐腐蚀性和与氟碳漆的附着力。缺点是磷酸的价格相对较高,且磷酸的酸性相对较弱,对铝合金表面的一些顽固杂质的溶解能力可能不如硫酸、盐酸等强酸。因此,在使用磷酸酸洗时,应根据铝合金表面的具体情况和对酸洗效果的要求,合理选择磷酸溶液的浓度、温度和酸洗时间。一般磷酸溶液的浓度为10%-30%,温度为50℃-80℃,酸洗时间为10-30分钟。酸洗后,应立即用大量清水冲洗铝合金表面,将残留的磷酸溶液冲洗干净,然后进行中和处理,以防止铝合金表面生锈。
铬化处理(可选):铬化处理是在铝合金表面形成一层铬酸盐转化膜的过程。这层转化膜具有良好的耐腐蚀性、性和与氟碳漆的附着力,能够进一步提高铝合金表面的防护性能和装饰性能。铬化处理的方法主要有浸渍法、喷淋法和刷涂法等,其中浸渍法是常用的方法。在进行铬化处理时,应根据铝合金的材质、表面状态和使用要求等因素,合理选择铬化液的配方、浓度、温度和处理时间等工艺参数。
铬化液配方:铬化液的配方通常由铬酸盐、氟化物、氧化剂、还原剂、缓冲剂等组成。不同的铬化液配方适用于不同的铝合金材质和表面状态,因此在选择铬化液配方时,应根据实际情况进行试验和筛选,选择合适的铬化液配方。
铬化处理工艺参数:铬化处理的工艺参数主要包括铬化液的浓度、温度、处理时间和pH值等。一般来说,铬化液的浓度越高,温度越高,处理时间越长,形成的铬酸盐转化膜的厚度越厚,耐腐蚀性和与氟碳漆的附着力越好。但是,过高的浓度、温度和处理时间也会导致铬酸盐转化膜的质量下降,如出现膜层疏松、龟裂、脱落等缺陷。因此,在进行铬化处理时,应根据铝合金的材质、表面状态和使用要求等因素,合理选择铬化液的浓度、温度、处理时间和pH值等工艺参数,一般铬化液的浓度为3%-8%,温度为30℃-50℃,处理时间为3-10分钟,pH值为2-5。铬化处理后,应立即用大量清水冲洗铝合金表面,将残留的铬化液冲洗干净,然后进行干燥处理,以防止铬酸盐转化膜生锈。
干燥处理:经过脱脂、酸洗和铬化处理后的铝合金表面,会残留一些水分,这些水分如果不及时,会影响氟碳漆与基材的附着力,同时也可能导致铝合金表面生锈。因此,在进行氟碳漆喷涂之前,需要对铝合金表面进行干燥处理。干燥处理的方法主要有自然干燥、热风干燥、烘干箱干燥等,其中热风干燥是常用的方法。在进行热风干燥时,应根据铝合金的材质、表面状态和尺寸大小等因素,合理选择热风的温度、风速和干燥时间等工艺参数,一般热风的温度为50℃-80℃,风速为2-5m/s,干燥时间为10-30分钟。干燥处理后,应检查铝合金表面的干燥程度,确保铝合金表面无水分残留。同时,应注意保持干燥后的铝合金表面清洁,避免再次受到污染。
氟碳漆涂装
底漆涂装:底漆是氟碳漆涂层系统的基础,其主要作用是增强氟碳漆与铝合金基材的附着力,防止基材生锈,同时为面漆提供良好的表面基础,使面漆能够地附着和发挥其装饰性能。常用的底漆有环氧底漆、聚氨酯底漆、丙烯酸底漆等,其中环氧底漆因其具有良好的附着力、耐腐蚀性和封闭性,是铝合金氟碳漆涂装中常用的底漆。
底漆调配:在进行底漆涂装之前,需要根据所选底漆的产品说明书和施工要求,将底漆、固化剂和稀释剂按照的比例进行调配。调配时,应先将底漆倒入干净的容器中,然后按照产品说明书上规定的比例加入固化剂,用搅拌器充分搅拌均匀,使其充分反应。后,根据施工要求和底漆的粘度,适量加入稀释剂,继续搅拌均匀,使底漆的粘度达到施工要求。底漆的调配比例应严格按照产品说明书上的规定进行,不得随意更改,以免影响底漆的性能和质量。同时,调配好的底漆应在规定的时间内用完,以免底漆发生固化反应,导致无法使用。
底漆涂装方法:底漆的涂装方法主要有空气喷涂、高压无气喷涂、刷涂、滚涂等,其中空气喷涂和高压无气喷涂是常用的方法。空气喷涂是利用压缩空气将底漆雾化成细小的颗粒,然后通过喷枪将这些颗粒均匀地喷涂在铝合金表面上。空气喷涂的优点是喷涂效率高,能够获得均匀、细腻的漆膜,适用于对装饰性要求较高的场合;缺点是对施工环境的要求较高,需要有良好的通风条件,同时漆雾的反弹和飞散会造成的浪费,增加施工成本。高压无气喷涂是利用高压泵将底漆增压至15-30MPa,然后通过喷枪的喷嘴将底漆喷出,在大气压力的作用下,底漆瞬间雾化成细小的颗粒,均匀地喷涂在铝合金表面上。高压无气喷涂的优点是喷涂效率高,能够获得较厚的漆膜,适用于大面积施工和对防护性能要求较高的场合;缺点是对施工设备的要求较高,需要配备高压泵、喷枪等设备,同时由于底漆的压力较高,对喷枪的操作要求也较高,如果操作不当,容易导致漆膜出现橘皮、流挂等缺陷。在选择底漆的涂装方法时,应根据铝合金的材质、表面状态、尺寸大小、施工环境和对漆膜质量的要求等因素进行综合考虑,选择合适的涂装方法。同时,在进行底漆涂装时,应严格按照所选涂装方法的操作规程进行操作,确保底漆的涂装质量。
底漆干燥:底漆涂装完成后,需要让底漆进行干燥固化。底漆的干燥固化时间主要取决于底漆的类型、配方、施工环境温度和湿度等因素。一般来说,环氧底漆的干燥固化时间在常温下(25℃)需要12-24小时,在低温下(5℃-15℃)需要24-48小时。在进行底漆干燥固化时,应注意保持施工环境的通风良好,避免施工环境中的湿度和温度过高或过低,影响底漆的干燥固化速度和质量。同时,在底漆干燥固化过程中,应避免对底漆表面进行碰撞、摩擦和污染,以免影响底漆的附着力和防护性能。底漆干燥固化完成后,应检查底漆的干燥程度和附着力,确保底漆表面干燥、无气泡、无针孔、无流挂等缺陷,且底漆与铝合金基材的附着力良好,符合施工要求。如果底漆表面存在缺陷或附着力不符合要求,应及时进行处理,如对底漆表面进行打磨、修补,重新进行底漆涂装等,直到底漆的干燥程度和附着力符合施工要求为止。
中间漆涂装(可选):中间漆是氟碳漆涂层系统中位于底漆和面漆之间的一层漆,其主要作用是增加涂层的厚度,提高涂层的防护性能和装饰性能,同时也可以对底漆表面的一些微小缺陷进行填充和修饰,使面漆能够地附着和发挥其装饰性能。在铝合金氟碳漆涂装中,是否需要涂装中间漆应根据具体情况进行综合考虑,如铝合金的使用环境、对涂层防护性能和装饰性能的要求、底漆的种类和性能等因素。一般来说,对于使用环境较为恶劣、对涂层防护性能和装饰性能要求较高的铝合金制品,如建筑幕墙、门窗、户外家具等,通常需要涂装中间漆;而对于使用环境较为温和、对涂层防护性能和装饰性能要求不是特别高的铝合金制品,如一些室内装饰品、小型电子设备外壳等,可以不涂装中间漆。
中间漆调配:如果需要涂装中间漆,在进行中间漆涂装之前,需要根据所选中间漆的产品说明书和施工要求,将中间漆、固化剂和稀释剂按照的比例进行调配。调配方法与底漆调配方法基本相同,应先将中间漆倒入干净的容器中,然后按照产品说明书上规定的比例加入固化剂,用搅拌器充分搅拌均匀,使其充分反应。后,根据施工要求和中间漆的粘度,适量加入稀释剂,继续搅拌均匀,使中间漆的粘度达到施工要求。中间漆的调配比例应严格按照产品说明书上的规定进行,不得随意更改,以免影响中间漆的性能和质量。同时,调配好的中间漆应在规定的时间内用完,以免中间漆发生固化反应,导致无法使用。
中间漆涂装方法:中间漆的涂装方法与底漆涂装方法基本相同,主要有空气喷涂、高压无气喷涂、刷涂、滚涂等,其中空气喷涂和高压无气喷涂是常用的方法。在选择中间漆的涂装方法时,应根据铝合金的材质、表面状态、尺寸大小、施工环境和对漆膜质量的要求等因素进行综合考虑,选择合适的涂装方法。